Day 1: Don’t try this at home, or in GMP (try it at the Testa Challenge!)
Like most systematic approaches, a failing cog, loose wiring or a single broken piece can cause the whole process to come to a halt. The same principle applies to bioprocess manufacturing. Thinking ahead and preparing for many months in advance, we have put several mitigations in place to keep the process going throughout the Testa Challenge week. We knew we were taking on a huge task and perhaps biting off more than we can chew, but no one could have ever been ready for what we were about to face. But the Testa Challenge is called a challenge for a reason.
October 19th 2020. It was a much colder morning than usual in Uppsala, colder than it had been in a long time in fact. The participants had arrived and were seated in the Testa Center ready to be taken through the safety regulations in order to begin their work in the labs. Things were slowly heating up…. everyone knew what they came here for, everyone was eager to start, everyone was excited.
It was now getting quite warm at the Testa Center. Cytiva staff and experts were at the ready and all the necessary lab preparations were complete to kick off the experiments as well as give a helping hand to the participants.
First in the lab was Fredrik Petersen, co-founder of atSpiro, starting up their ShakeReactor, a shake flask bioreactor, in the Kuhner SFI-XC shaker. Our first challenge of the day was the speed and stability of this step. Not having had access previously to a standard industrial shaker with a large throw diameter, this was a learning for atSpiro. If the flasks are not secured properly or the shaker would be set at too high RPMs, the flask could fall over due to the new weight distribution of flask and ShakeReactor. After a brainstorm and while maintaining a cool head, the atSpiro team with the experience and well as intuition of Andreas Anderson, the project technical lead, realized what adjustments need to be made. Adding further securing measures and lowering the RPMs the flask was securely fastened and ready to operate optimally.
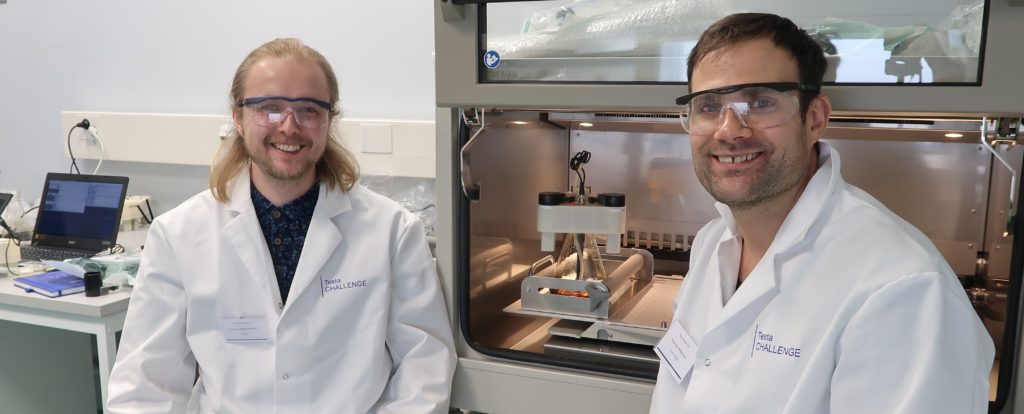
Within the next hour we faced our next hurdle: the integration of the sensor-ball innovation from Freesense into the sterile GMP-graded single-use bioreactor bag. To accomplish this, we needed to cut open the bag and insert the sterilized sensor-balls. Patricia Roch, an expert from Cytiva, was overseeing this task as well as the complex procedure of re-sealing the bag using a heat gun. With much concentration and skilled hands, Patricia only had few words of wisdom while bringing the bag back into operational conditions under the sterile laminar flow hood, “Don’t try this at home, or in GMP”.
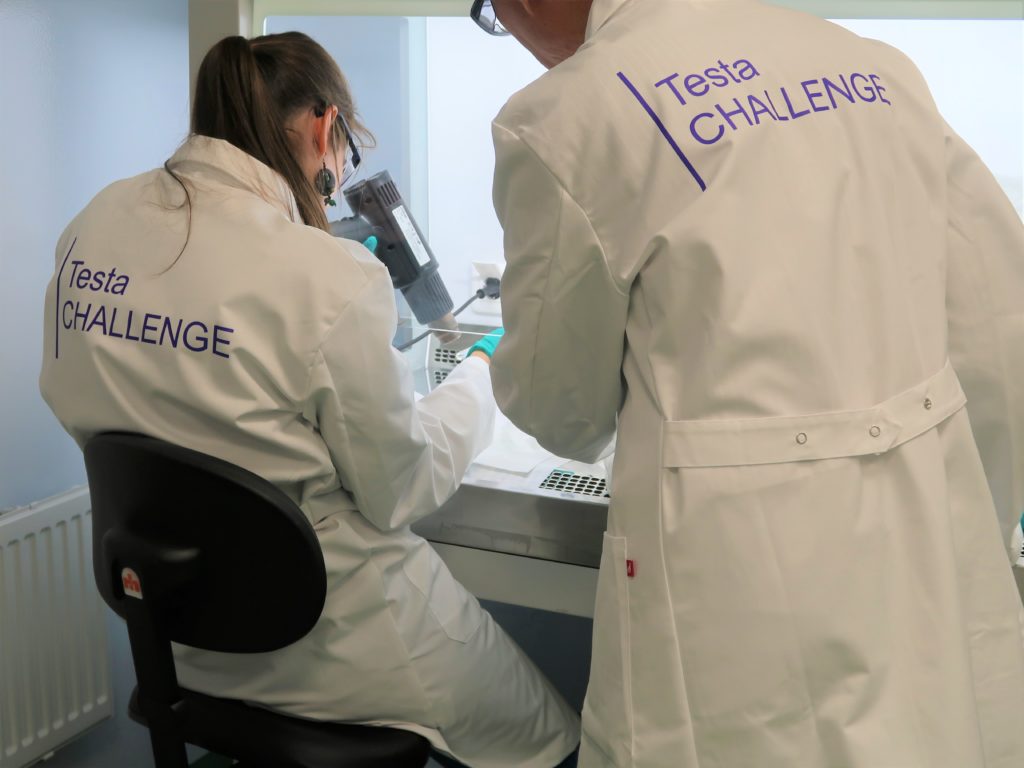
"Don't try this at home, or in GMP."
Patricia Roch, 2020
After five minutes the Testa Center certainly became one of the hottest places for Andreas as his face turned white and sweat was building up on his forehead. There were incorrect readings coming from the pH-probe and error messages. This could put the whole cell culture in jeopardy and would be a catastrophe for the Testa Challenge and Freesense’s data.
Or so we thought. After closer inspection, we found out that we needed to reset the pH-probe. With a swift and easy hand Andreas reset and recalibrated the pH-probe. With an updated schedule for the week we were ready to continue. Things finally began to cooldown again at the Testa Center.
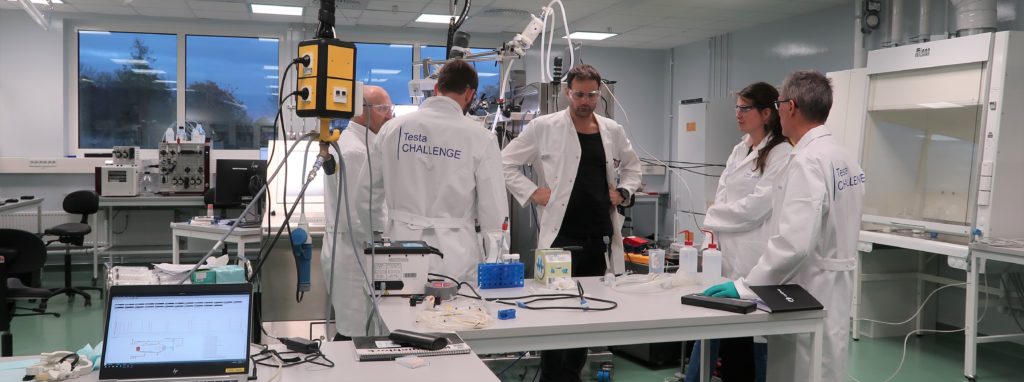
After an intense and very interesting first day of the Testa Challenge we concluded that it’s always a lot of fun to work at the Testa Center. Even though it might not always go as planned and late nights in combination with early mornings are needed; this is how innovation is made and how we push the boundaries to make it happen.
Are you into technology in life science and bio-process, make sure to contact Testa Center to learn how you might accelerate your project together with us!